Making New Mirrors
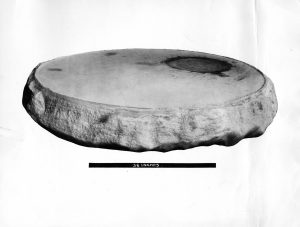
This doesn’t look like much, but it was the start of something that was going to revolutionize the field of astronomy. This is a disk of silicon dioxide, also known as silica. Since it is made from very clean quartz sand, it is also known as “fused quartz”. You can think of silica as being very pure glass without any additives.
Those additives serve a purpose. They lower the melting temperature of the silica. Without those, silica can require a furnace at 3,000 degrees Fahrenheit to work with. But removing those additives means that you have a type of glass that is very resistant to changes in temperature.
One of the first people to see the advantages in this was Elihu Thomson, a scientist, engineer and businessman who founded the Thomson-Houston Electric Company. This company later merged with Edison General Electric to create the General Electric company we’re familiar with today.
Since fused quartz is so resistant to heat, it has been used in high temperature applications like halogen lamps and furnaces. It’s strong, so it has been used in bathyspheres and other high-pressure devices. But Thomson was an avid amateur astronomer, and he saw a use for silica that others might have missed: telescope mirrors.
Since silica resists changing shape with heat, it could be used in unheated observatories that could get blistering hot or freezing cold without distorting the viewing. It could also resist the heat produced by grinding and polishing, which made it easier and faster to work with that regular glass. Mirrors could be produced faster and – more importantly – larger than ever before.
In the late 1920s, when George Hale convinced the Carnegie Institution to fund the construction of a new telescope for the Palomar Observatory, he was thinking big. Hale had already worked on the largest telescope in the world: the 40-inch refracting telescope at Yerkes Observatory, 60-inch Hale reflecting telescope at Mount Wilson Observatory and 100-inch Hooker reflecting telescope at Mount Wilson. For his next – and final – telescope, he would require a massive 200 inch mirror.
This was probably beyond the conventional technology of the time. Hale needed to try something new. He ended up turning to Elihu Thomson and his idea for a fused silica mirror.
The lump at the upper right was a proof of concept. The next mirror would be a sixty inch disk, and no one had worked with silica on that scale before. It required new techniques and the construction of new furnaces in Thomson’s Lynn, Massachusetts plant.
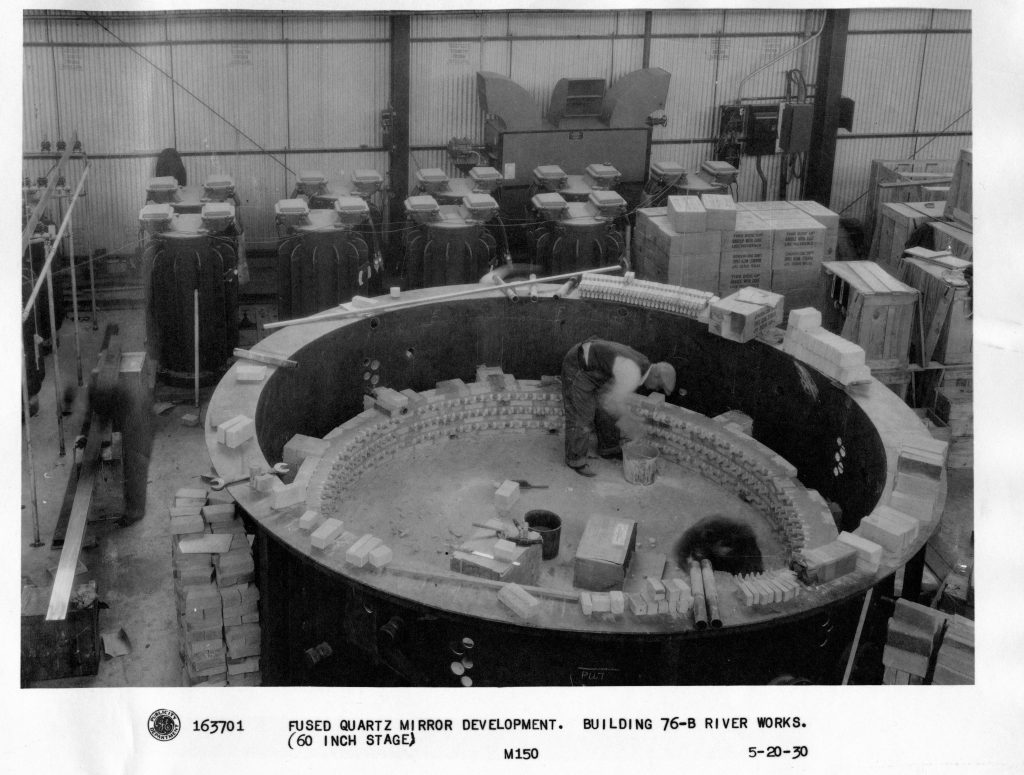
In the end, it took three years to produce two sixty-inch mirror. The first mirror was of excellent quality, but it cracked during the cooling process. The second mirror was marred by air bubbles. Thomson and General Electric had proven that large scale silica mirrors could be made, but that wasn’t enough. Hale needed something produce quickly, and at a reliable price.
So the 200-inch mirror was not made in a Schenectady factory, but in Corning Glass works. And instead of silica, it was made of Pyrex. One of the first attempts at the 200-inch mirror is on display at the Corning Museum of Glass.
It’s a little frustrating, but it’s a good example of the difference between a new technology and a more mature technology. Pyrex had been invented in the 1890s, about the same time that Thomson began experimenting with fused quartz. But Thomson was a businessman, and a busy one. There was no immediate need for silica mirrors, and the potential market seemed small. General Electric had plenty of other things to do.
Corning invested more time and energy into Pyrex, and so they went into the process with more confidence. They succeeded in six months when GE it had taken three years to not quite pull it off.